パナソニック コネクトになって「Let's note」は変わる? 変わらない? シン・ウルトラマンとの関係も聞いた(2/3 ページ)
Let's noteを扱うパナソニック・コネクティッドソリューションズ社が、2022年4月にパナソニック コネクトに生まれ変わった。新会社の現状とLet's noteを生産する神戸工場について、同社副社長と工場長に話を聞いた。
神戸工場の現場はどう変わった? 神戸版スマートファクトリー?
―― 新型コロナウイルスの拡大以降、工場内では従来と違った対応を求められたり、異なる対策が必要になったりしたかと思います。
矢吹氏 最初の緊急事態宣言の前後から、当社トップの樋口が積極的にビデオ会議を行い、事業部長の坂元も定期的にメッセージを発しましたが、一方通行にならないよう双方向のやりとりを意識しました。例えば、メッセージに対してアンケートを取ってフィードバックをして、それを坂元が受けて答えていくなど連係を密にして、工場の意見を伝えられるよう繰り返し行いました。
残念ながら、コロナ禍でも工場自体はリモートワークができないため、対策を徹底するということを常に意識しました。例を挙げると、以前は検温をする習慣がありませんでした。出社するのであれば、まず自宅で検温するようにと伝えたのですが、なかなか徹底されません。そこで、私が自ら工場の入口で従業員の検温を実施したりしました。
やはり、みんなが安心かつ安全に働いてもらう環境を整えるには、全員が意識を徹底する必要があります。その意識を持ってもらうべく、あえてアナログな手法を取り入れて習慣化まで持って行きました。
工場内では絶対にクラスターを出してはいけないと、透明性を高めるべく積極的に情報発信し共有もしています。食堂も交代制にしたり、対面にならないよう座席の配置を工夫したりと、細かいところまで配慮して、分かりやすく意識してもらえるようにしています。
―― 以前は、工場見学もリアルがほとんどだったと思います。
矢吹氏 2019年までは、年間2000人以上の方々が見学に来られていましたが、2020年には1000人規模にまで縮小しました。しかし、お客さまと接点を持つことは非常に大切なことであり、新たな取り組みとしてリモート工場見学をスタートしました。これをブラッシュアップしていくことで、2021年にはリアルを含めて1850人まで回復し、2022年は今のところ2000人ペースで推移しています。
逆に、リモート工場見学を進めることで、従来以上に海外のお客さまとの接点が増えました。当初は、文字通り現場にカメラを持ち込んでライブで映像を送っていましたが、海外だと回線の状態も不安定で落ち着いて見学できない場合もあったので、映像を編集して1つの1つのパッケージにして動画を見られるようにしたりしました。
今後も、お客さまのご要望に応じてリアルとリモートを選んでいただけるよう、接点の選択肢を増やしていきたいと思っています。
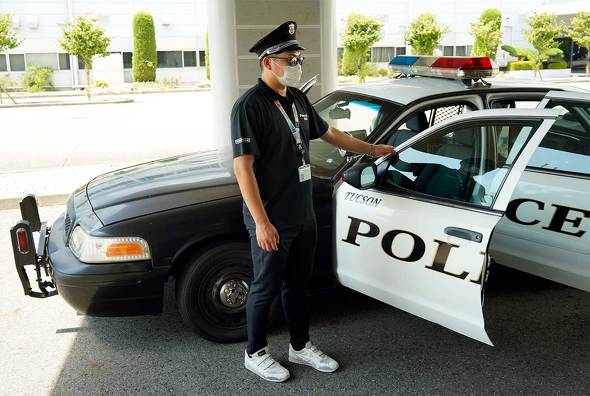
米国で現職の警察官のコミュニティーがあって、熱心な警察官が工場見学に来られたのが印象的だったという。写真は手づくりレッツノート工房の見学コースに含まれている、TOUGHBOOKを車載した米国で利用されたポリスカー(車内にTOUGHBOOKが装着されている)の試乗体験風景
―― 2019年8月に工場長に就任してから取り組まれている、神戸工場でのスマートファクトリー化の取り組みはいかがでしょうか。
矢吹氏 日本の労働人口が減少していく中で、省人化を目的にIoTやAIを駆使したスマートファクトリー化は重要な取り組みです。ただ、就任当時に比べて世の中の環境が大きく変わってきており、それに応じて中身もだいぶ変わってきています。
例えば、コロナ禍で半導体が不足し、サプライチェーンも分断されている中で、どのように対応していくのか。一緒になったBlue yonderのソリューションを活用していこうと進めています。
もう1つは、人と機械の役割を明確にした上で工程ごとに最適な融合を目指す「人と機械の融合」があります。基板の実装やチェック工程では、以前は人が行っていましたが、静電破壊や基板を落として壊してしまうのを回避すべくロボットを活用しています。
一方で完成組み立て工程は人が行い、品質を保証する最終検査は人の判定によるブレやポカミスをなくすべく自動化(ロボット化)しています。これからは組み立て工程も自動化を進めていきたいですが、まずは検査工程の省人化を優先しています。
キーボードの入力検査は、エラーを見つけるのが目的ではなく直行率(工程における良品割合)を高めるのが目的だ。エラーの原因を見つけてすぐにフィードバックを行っており、このFVシリーズで導入してうまくいったものを他のシリーズにも横展開しているという。段階的に機械化を進めており、部品の運搬作業の自動化も推進している。
いわば人が持つ匠(たくみ)の技を継承しつつ、人だけには頼らない神戸工場のならではのスマートファクトリー化が着々と進んでいるようだ。
最後に、話題を集めた映画との関わりを聞いた。
関連記事
“元祖”と“完全国内生産”の自信に裏打ちされた「手づくり工房 2019」で感じたLet's noteのプライド
パナソニックが、毎年夏休みに実施しているLet's noteの組み立てイベント「手づくりレッツノート工房 2019」が8月3日に開催された。本イベントに込められた同社の思いとは何か。最年長参加者が組み立てたLet's noteは無事起動したのか
毎年夏休みに、パナソニックが自社工場で行っているLet's noteの組み立てイベント「手づくりレッツノート工房 2019」。50組の親子に交じって飛び入り参加をした編集者の行方は……。第12世代Core採用でハイブリッドワークに最適化した14型モバイルPC「Let's note FV3」を使って分かったこと
パナソニック コネクトの人気モバイルPC「Let's note FV」シリーズに、第12世代Coreを採用した新モデル「Let's note FV3」が加わった。直販のプレミアムモデルをチェックした。ハイブリッドワークにフィットするシリーズ1番人気モデルがWindows 11で登場 「Let's note FV1」を試す
パナソニックの14型モバイルPC「Let's note FV」 シリーズが、Windows 11を搭載して生まれ変わった。アスペクト比3:2の画面を備えた見どころの多い最新モデルをチェックした。パナソニック コネクト、第12世代Core i7を搭載した14型ノート新モデル「FV3」など2022年夏モデル4製品を投入
パナソニック コネクトは、モバイルノートPC「レッツノート」の2022年夏モデル4シリーズの発表を行った。
Copyright © ITmedia, Inc. All Rights Reserved.