後編 MADE IN JAPANの“360度こだわりUltrabook”を解剖する:「FMV LIFEBOOK UH75/H」完全分解&開発者インタビュー(3/5 ページ)
2回に渡ってお届けする「FMV LIFEBOOK UH75/H」の開発者ロングインタビュー。後編は実機を分解しつつ、“HDD搭載のUltrabookで最薄”を実現した内部の作り込みに迫る。
最後まで苦労させられたバッテリーとヒンジ
―― ボディ内部には余分なスペースがありませんが、各パーツがすっきりレイアウトしてある印象です。内部のレイアウトはどのように決めたのでしょうか?
松下氏 これはもう……、何度も何度もやり直しました(笑)。
小中氏 短い開発期間でガラガラポンと3回は大きく変わっています。最初の課題は大容量のバッテリーをどうやって入れるかでした。バッテリー駆動時間は9時間が目標、あわよくば10時間を狙っていましたが、それだけの容量を確保しようと思うと、バッテリーのサイズは大体決まってきます。
現状でUltrabookに適しているリチウムポリマーのバッテリーセルは、それほど種類が多いわけではないので、バッテリーメーカー数社に目的の駆動時間に見合う容量のサンプルをいくつか作ってもらい、検討を重ねました。
その後は何とか2つの候補に絞り込み、第1候補で開発を進めていたのですが、2011年10月の内部レイアウトを固めなければならない土壇場というところで、第2候補に急きょ変更しました。最後のほうまでバッテリーには苦労させられましたね。
そのかいあって、厚さや奥行きの寸法を目標値から変えず、容量45ワットアワー(14.4ボルト 3150mAh)のバッテリーで約9.1時間の駆動時間を達成しています。急速充電に対応していて、1時間で約80%充電できるのもポイントです。さっと充電して長時間使っていただけると思います。
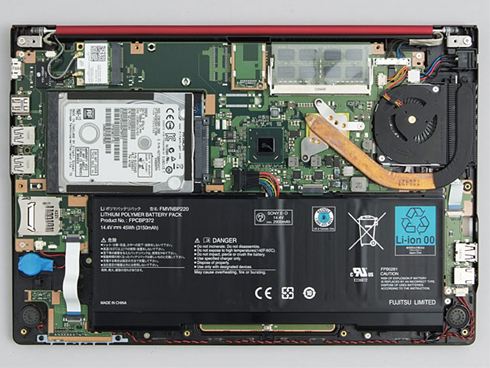
―― 最終的にバッテリーを変更した理由は何だったのでしょうか?
小中氏 バッテリーの容量を大きくできたことと、構造をシンプルにできたことが、大きな理由です。
バッテリーのサイズを冷静に考えた場合、バッテリーセルは小型化のしようがありませんが、安全性を保つ回路の部分は若干薄くできます。そこで、試行錯誤の末、バッテリーパックの回路部分のみを薄くして角を斜めに落とし、ボディの先端から厚みが増していくフォルムを追いかけるような形状に仕上げてもらうことで、目標値からギリギリはみ出さずに詰め込むことに成功しました。
今回はあまり後先考えずに理想を求めて、最初のモックアップで奥行きの寸法を決定してしまったわけですが、実際にバッテリー、HDD、その他モジュールと長さを足していくと、奥行きがどうしても目標値に入らず、奥行きを長くすべきか、という誘惑に負けそうになることもありました。デザインの担当から「奥行きを増やすなんてあり得ない」という話もあり、何とか踏みとどまりましたが(笑)。
―― バッテリー以外で特に苦労された部分はありますか?
小中氏 意外に思うかもしれませんが、バッテリー以上に最後まで引っ張ったのは、液晶ディスプレイのヒンジ部分でした。
ノートPCに使われる液晶ディスプレイのヒンジは、左右の2点で支えるタイプと、中央に長くスペースを取って軸を入れたタイプの2つがあります。我々は「万歳ヒンジ」と呼んでいるのですが、2点で支えるタイプならば、ヒンジの周辺に部品を並べるスペースを少しでも作れるため、今回のような余裕のない設計には都合がいいわけです。
そこで、最初は万歳ヒンジで開発を進めていたのですが、2011年の12月中旬になって「この通りに作ると豪語したモックアップと、違うデザインになっているではないか」とパーソナルビジネス本部の上層部から指摘がありました。そうなんです。モックアップでは長い軸を入れたタイプのヒンジだったのが、そのままだと奥行きが入らないので、勝手に万歳ヒンジに変えてしまったのです。
それで「もう、こうなったら作り直すしかない」と決意を固めたのですが、ボディの寸法はもう動かせないため、基板を小さくすることで、ヒンジのデザインをモックアップ通りに仕上げました。
具体的には基板の最終確認をする予定の1週間前に、基板を5ミリ縮めるというチャレンジをすることになったわけです。1週間で5ミリ縮めるのはさすがに参りましたが、何とかやり遂げました。
独自のプリント基板設計CADとデータ共有で開発を効率化
―― ほぼ完成した基板、しかもUltrabook用に余分なスペースなどない基板をヒンジのデザインのため、1週間で5ミリも縮めるなんて通常では考えられませんが、よくできましたね。
小中氏 もう気合の世界ですが(笑)、ここでもF-07Cの開発で突き詰めた小型化のノウハウが役に立ちました。ケータイの開発では既に実績がある自社製のプリント基板設計CADをUH75/Hに導入して、CADのスピードアップを図ったことが大きいですね。
今回の開発では超圧縮デュアルグリッド構造も含めて、内部の部品同士をすき間なく配置するため、あらかじめ関係部署で3D CADデータの共有を進めていました。構造設計からデザインまで、同じCADデータを共有したことにより、ボディデザインを崩さずに基板を収める、グリッドの桟に干渉しないように部品を並べる、といった細かい作業を効率よく短期間で行ってきたわけです。
1週間で5ミリ基板を縮める作業にあたっては、CADを操作しながら、全面コピーで基板を5ミリ下に移動させ、次に動かせない部品を上に戻し、あとは少し下のほうにあるコネクタなどを少しずつググッと詰めていきました。すると、できるだけ他への影響を少なくしつつ、基板を5ミリ縮められそうだと1日くらいで目鼻が付いたので、1週間で何とか修正して最終データ出しまでこぎ着けました。年末の発売半年前になって、ようやく設計が終わったことになります。
2012年の年明けからも慌ただしかったです。1月初旬に、実際にちゃんと動作するのか確認するマスターを作り始めました。1月末にケースが初めて上がってきて、ちょうどその頃に紆余(うよ)曲折で完成した基板も届いたので、それを組み合わせて、ようやく2台程度のマスターができたという状態です。
マスターの数が少ないため、2月末くらいまではケースのない基板とパーツが丸出しの状態でも評価を続けました。1月末に金型を起こし、2月にケースができて3月に届き、3月中旬にケースを付けた試作機がようやく完成します。そこから確認作業を進めて、4月末に量産を開始、5月9日に製品発表会、6月7日に発売という流れです。実物のケースを見てから発表まで2カ月しかないような非常にタイトスケジュールでしたが、何とかこなせました。
―― 相当厳しいスケジュールでの開発に思えますが、ここまで短期間でゼロから製品開発を行うようなことは、過去のFMVにもあったのでしょうか?
小中氏 いや、ここまでタイトなスケジュールは初めてです。もともと実績がある製品で開発期間を短くすることはありますが、まったくの新しい製品をここまでこだわりつつ、短期で作り上げるというのは前例がないですね。
関連キーワード
Ultrabook | 富士通 | ノートPC | FMV | FMV LIFEBOOK | FMV LIFEBOOK UH | メイドインジャパン | モバイルPC | プリント基板 | SanDisk(サンディスク) | Intel Rapid Start Technology | WEB MART
*** 一部省略されたコンテンツがあります。PC版でご覧ください。 ***
Copyright © ITmedia, Inc. All Rights Reserved.